Model No. | No. of Elements | Size of Element (inch) | A (inch) | B (inch) | C (inch) | D (inch) | Inlet/Outlet Connection | Drain Outlet Connection | Max Flow Rate (US GPM) |
---|---|---|---|---|---|---|---|---|---|
SAB-BCM300 | 8 | Φ2.25*25.6 | 53.1 | 10.4 | 35.6 | 11.8 | 4” | 2” | 310 |
SAB-BCM400 | 12 | Φ2.25*25.6 | 55.9 | 10.4 | 37.2 | 15.7 | 6” | 2” | 660 |
SAB-BCM500 | 22 | Φ2.25*25.6 | 59.8 | 11.4 | 39.4 | 19.7 | 8” | 2 ½” | 1100 |
SAB-BCM600 | 30 | Φ2.25*25.6 | 63.0 | 11.4 | 40.2 | 23.6 | 10” | 2 ½” | 1750 |
SAB-BCM700 | 30 | Φ2.75*25.6 | 66.9 | 13.2 | 41.3 | 27.6 | 12” | 3” | 2650 |
SAB-BCM800 | 38 | Φ2.75*25.6 | 70.9 | 13.2 | 41.3 | 31.5 | 14” | 3” | 3500 |
SAB-BCM1000 | 50 | Φ3.35*31.5 | 84.6 | 13.2 | 45.3 | 39.4 | 16” | 4” | 5300 |
SAB-BCM1200 | 76 | Φ3.35*31.5 | 92.5 | 14.4 | 49.2 | 47.2 | 20” | 4” | 8000 |
SAB-BCM1400 | 100 | Φ3.35*31.5 | 98.4 | 17.3 | 54.5 | 55.1 | 24” | 4” | 11,000 |
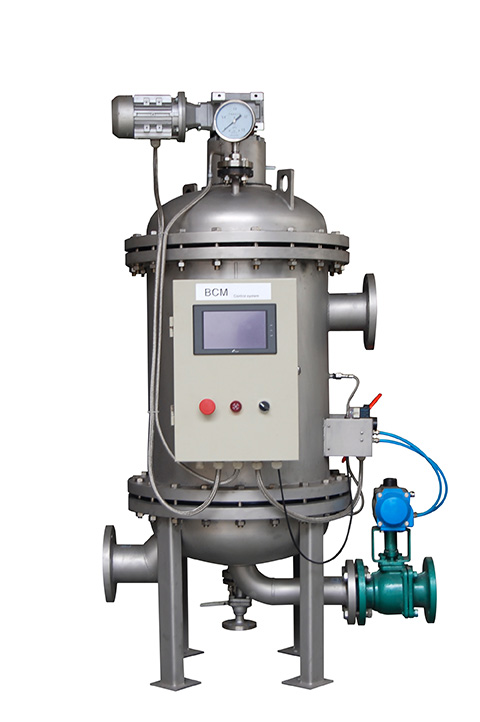
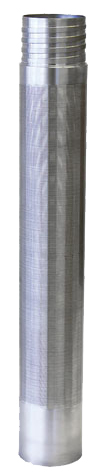
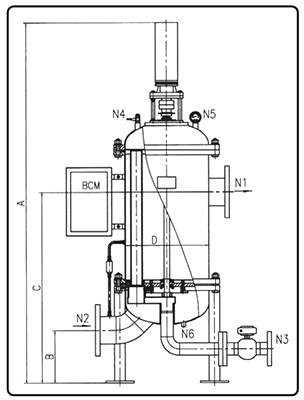
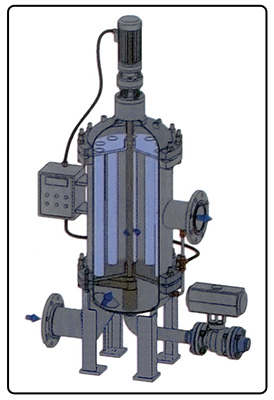
Automatic Backwashing Self-Cleaning Filter Systems – BCM Series
Description of Normal Operation: This automatic filter system is used to filter low-viscosity, large flow and high-speed fluids. BCM automatic filters are widely used in metallurgy, chemical industry, power industry, re-injection of water in oil field, ballast water in shipping industry and water treatment. The automatic filter system consists of a main housing, gear motor, inlet and outlet ports, filter screen elements, a drain valve, pneumatic actuator, pressure differential meter, and a control system.
I. PROCESS
The process begins with fluid flowing through the inlet. The fluid enters the filtration screen through a fixed plate at the bottom of the filter. Then, the fluid flows from the inside of the screen to the outside. As the fluid flows through the wedge-wire filter screen elements, solid impurities that are larger in size than the screen’s micron rating become trapped on the inside of the screen. The filtered fluid exits the system through the outlet. As the impurities accumulate on the inside of the screen, a pressure differential is created, and will continue to increase between the contaminated and clean sides.
II. CONTROL PANEL MODES OF OPERATION
Automatic Operation:
Pressure Setting
- The automatic filter’s control system monitors the rising differential pressure.
- The automatic filter systems are equipped with a pressure differential meter through which the end-user sets the differential pressure requisite (i.e. pressure dependent setting) to automatically start the backwash cycle. When this differential pressure is reached, the control system sends a signal to start the backwash cycle
Time Setting:
- The backwash cycle can be initiated at pre-defined time intervals.
- Pressure dependent settings takes precedence over time dependent settings.
Manual Operation:
- The primary usage is for commissioning and testing.
- The backwash cycle can be started by pressing the ‘TEST’ button.
- In manual mode, there are no pressure or time setting controls.
III. BACKWASH CYCLE:
- The backwash cycle cleans one element at a time, in succession.
- The gear motor is connected to the middle shaft and drives the cleaning arm to the element being cleaned. A photoelectric positioning switch controls the rotation angle of the cleaning arm.
- The drain valve is then opened by a pneumatic actuator which draws clean filtered fluid from the outside of the screen to the inside, whereby the impurities are flushed down into the drain line.
- When the length of the backwash cycle is reached, the drain valve closes and the backwash cycle for this element is completed. The gear motor then drives the cleaning arm to the next element and the backwashing cycle restarts.
- After all the system’s elements are backwashed, the cleaning arm returns ‘Home’ and the backwashing cycle has been completed.
- When the drain valve opens, the filter system momentarily uses a negligible amount of clean fluid to backwash.
Design Advantages and Features:
- Automatic online continuous filtration – the automatic filter system does not have to be taken offline to enter the cleaning mode because the backwash cycle cleans one screen at a time, thus enhancing the end-user’s profitability and overall productivity. All other screens remain on-line and continue filtering the fluid.
- A gear motor is used to drive the automatic filter system.
- The unique and innovative internal structure ensures delivery of a high quality backwashing and filtration system.
- Provides the end-user with long term operation and precision filtration with no flow interruption. Impurities are easily flushed away from the filter screen.
- The automatic filters are equipped with wedge wire screen elements and are available in various materials including 2205 and MONEL. These elements provide precision filtration (as fine as 50µm), are corrosion resistant, and sustain much more wear and tear.
- Cost effective, easy to operate, requires minimal maintenance and is environmentally friendly – these automatic filters do not require the end-user to purchase, change-out or dispose of any bags or filter screens.
- The control system can be tailored to monitor pressure and time settings for various fluids (i.e. the BCM automatic filter system is flexible).
- Compact design – installation requires minimal space and is easy to install. The inlet and outlet ports are adjustable according to the end-user’s requirements.
Applications:
- Seawater desalination
- Recycling of cold water
- Water re-injection in oil fields
- Ballast water in shipping industry
- Recycling of flash steam from boiler
- Pre-filtration for ultra-filtration and reverse osmosis
- Pre-treatment of ion exchange
- Nozzle filtration in pulp & paper industry